
You will also learn about the use of simulation for risk studies to enhance process resilience, fault finding in abnormal situations, and for training operators to control the process in difficult situations. Content coverage includes steady and dynamic simulations, the similarities and differences between process simulators, an introduction to operating units, and convergence tips and tricks. This book will help you predict the characteristics of a process using mathematical models and computer-aided process simulation tools, as well as model and simulate process performance before detailed process design takes place. This gives new customers a great deal of confidence in our ability to design and deliver a plant to their specifications.Chemical Engineering Process Simulation is ideal for students, early career researchers, and practitioners, as it guides you through chemical processes and unit operations using the main simulation softwares that are used in the industrial sector. We can simulate a model of a production plant and show that the simulation results match the actual performance of the plant.
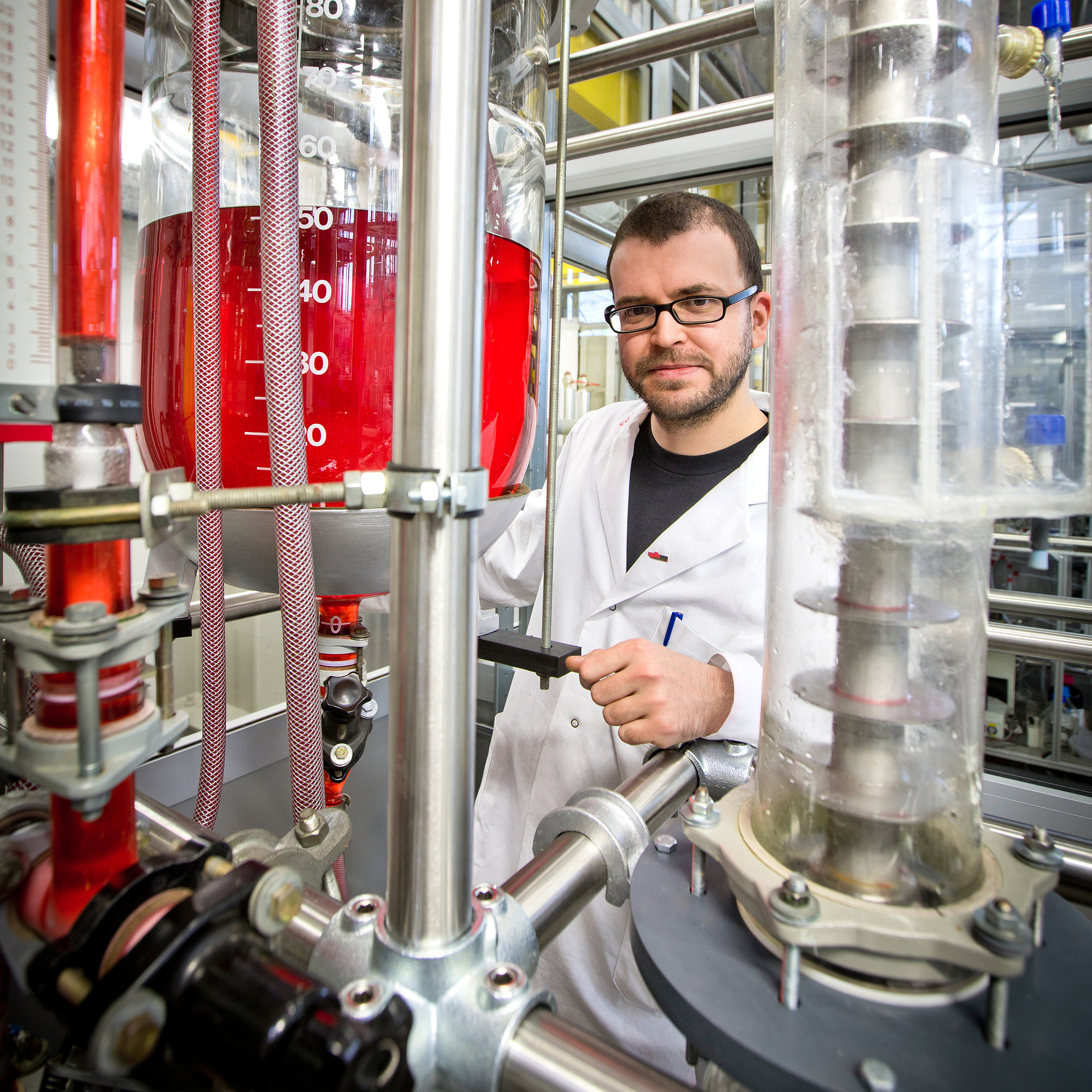
This approach has made it easier to demonstrate plants and new design concepts to our customers. Just as importantly, quality has increased, as we now can find and eliminate errors much faster. We have designed and simulated systems-including the largest oleum plant in the world-that were far too complex to handle with our spreadsheet-based approach. Overall, MATLAB and Simulink have enabled us to cut costs and reduce development time by a factor of 5 to 10. The shared environment has improved communication between the control and chemical process engineers, making it easy to collaborate to solve problems and optimize performance. Because the designs we create are flexible, we can quickly respond to changing customer requirements. Model-Based Design with MATLAB and Simulink has enabled us to evaluate many design ideas for each project.
#Chemical process simulation degree code#
Our process engineers can use the blocks by simply dragging and dropping them into the Simulink environment, but they can also study the underlying MATLAB code and develop new MATLAB classes, as well as create new libraries in Simulink. The outputs of the absorption tower model, one gas object and one fluid object, capture the results and are used as input to the next subsystem in the plant. The classes perform all the operations that were previously done in spreadsheets, as well as several new calculations that were enabled by the switch to MATLAB-for example, calculation of the heat generated by the absorption of SO3 in different concentrations of sulfuric acid. We modeled the thermodynamic and kinetic processes in MATLAB using the classes we had developed. In the actual tower, the gas enters at the bottom of a column and is partially absorbed by the liquid, which enters through the top of the tower and runs down through the column. To manage the overall complexity of our designs, we defined each module as a MATLAB class, enabling us to apply object-oriented design patterns to the development of the entire library.Īn absorption tower, for example, is defined as a MATLAB class, as are the fluid and gas streams that it takes as input. The first step in the new workflow was to create a library of reusable modules, one for each subsystem, which the chemical process engineers could then combine in Simulink system models. The new approach is 5 to 10 times faster than the spreadsheet-based approach, and much less susceptible to human error. The plant and its control system can then be tested in dynamic and steady-state closed-loop simulations. While the chemical process engineers model the complex thermodynamic and kinetic interactions within the plant, controls engineers model the control algorithms. Model-Based Design with MATLAB ® and Simulink ® has provided a cost-effective way to simplify and automate our design workflow by enabling chemical process engineers and controls engineers to work in the same environment.
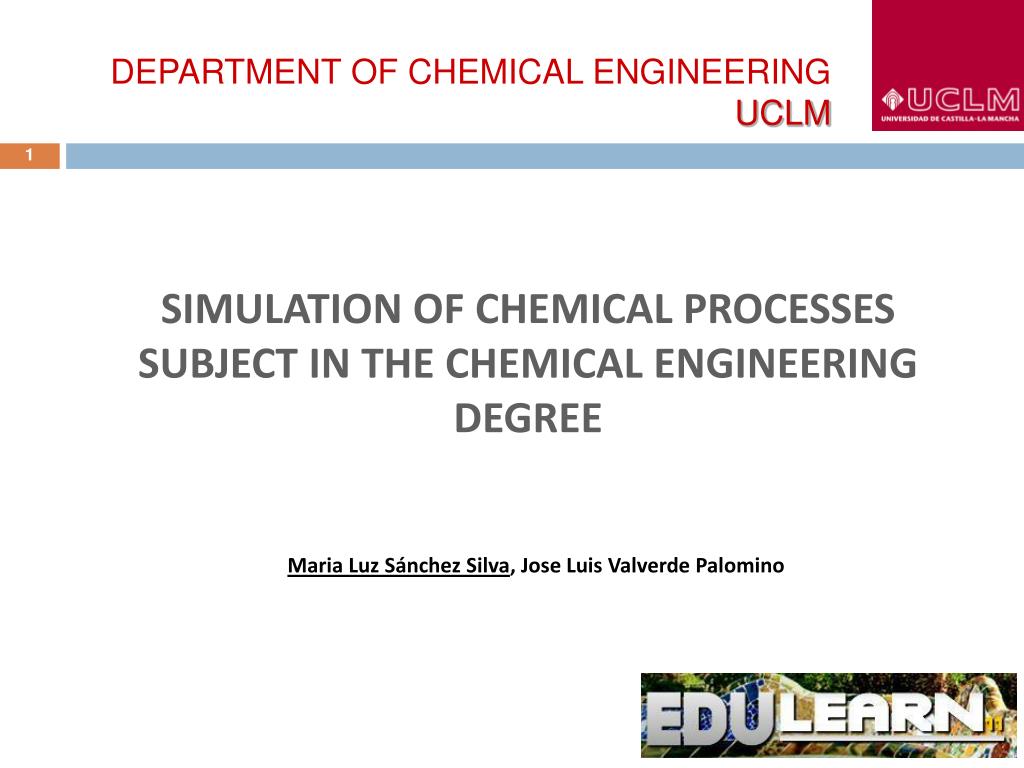
#Chemical process simulation degree manual#
This manual approach slowed development and introduced the potential for human error.

All preliminary design work and process modeling was done using a complex system of spreadsheets. Until recently, however, our development process was highly labor-intensive. HUGO PETERSEN GmbH has a decades-long track record of engineering safe and efficient sulfuric acid and gas cleaning plants. Used acid and waste gases are recycled in processing plants that must meet stringent safety and environmental requirements for working with these chemicals. Sulfuric acid is used in the manufacture of fertilizers, petrochemical products, synthetic fiber, steel, and a wide range of other industrial materials.
